An epiphany that led to efficiency improvements across a continent
Our Trouw Nutrition North America team lowers emissions by optimising boiler efficiency
Our Trouw Nutrition team in North America had an “Aha!” moment when they realised that 80% of the region’s emissions come not from propane forklifts, not from diesel trucks, but from natural gas –– and nearly 100% of this natural gas was used to create steam for their plants’ pelleting process. What better place to start reducing emissions than in the steam boilers used in all 19 of their feed production facilities?
First, the team thought of making the switch to electric boilers, but that came with a prohibitive cost, and a long payback. So, they decided a better approach would be to make the current boilers more efficient, for example, by adding a deaerator, or upgrading the burners to optimize boiler performance. The team evaluated every plant and determined which solution would work, based on the age of the boiler and the needs of the location.
So far, they’ve optimised around 68% of the boilers and it is already making an impact. For example, the team has installed a deaerator system in a plant in New Brunswick, Canada, that removes oxygen from boiler feedwater, decreasing the need for chemicals and reducing corrosion to maintain energy efficiency. The deaerator enabled them to reduce CO2 emissions by about 92 metric tons in 2023. That’s the emissions equivalent of over 50 round trip flights from London to New York!
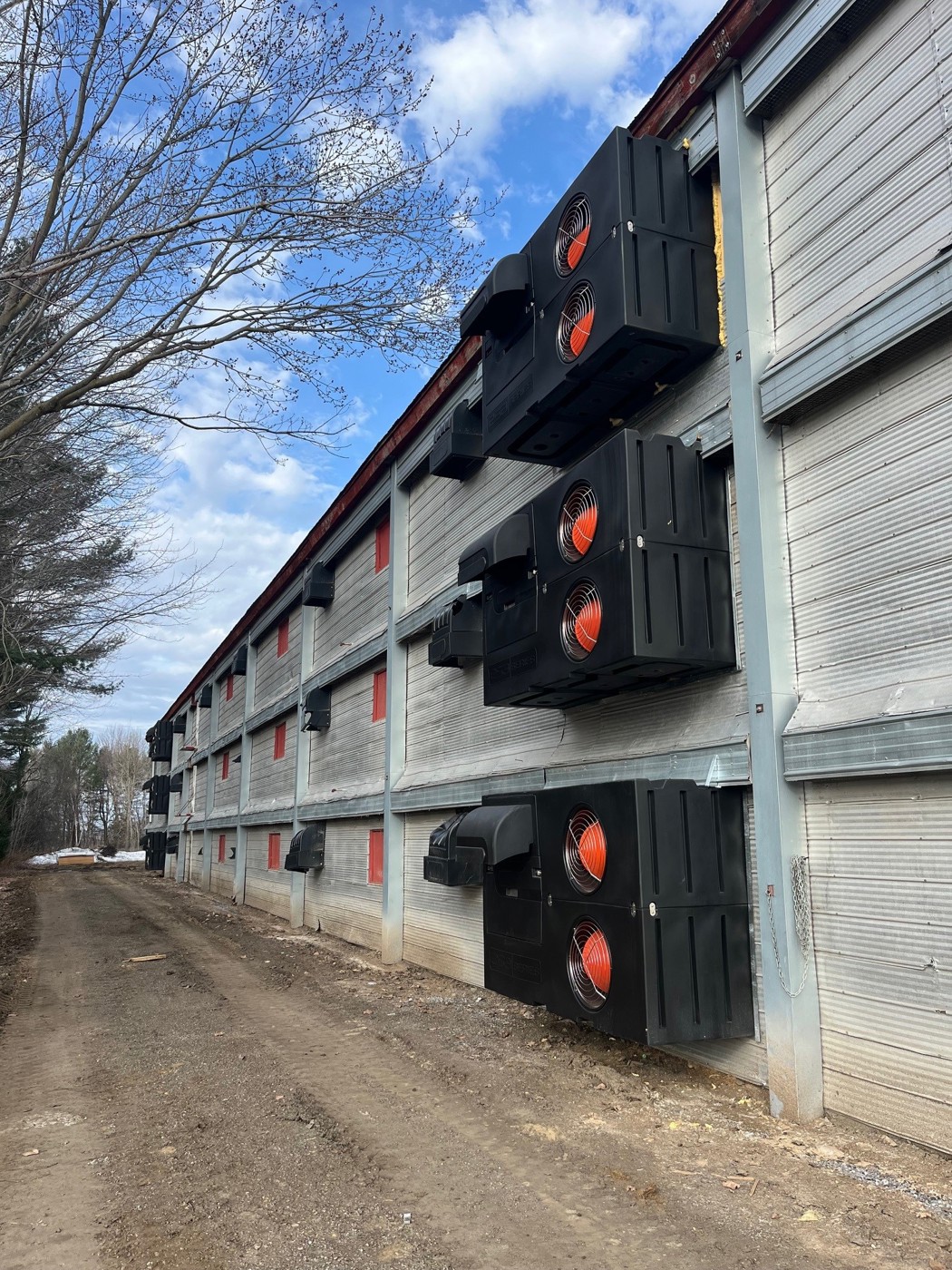
They’re replacing old and inefficient equipment with new, more efficient units that use improved technology. For example, by replacing old and inefficient pellet mills in the Hill Country, Texas, facility, they were able to reduce power consumption by 22%.
The team is not only optimising equipment in the feed mills but also in their poultry operation – namely in the Baril Farm in Quebec. They are transitioning over to electric air exchangers in the hatchery, for a projected CO2 reduction of 232 metric tons per year. That’s enough CO2 to fill up 59 hot air balloons!
They plan to continue these efforts for the next two to three years, and then determine whether the economics and technology have shifted to make going fully electric more viable.
The continuous efforts of the team are inspiring! It shows that the continuous strive we have to be competitive, and serve our customers properly, goes hand in hand with taking our responsibility for the environment to reduce our emissions. The solutions are out there, and I think it is fantastic the team is adopting them one by one. Big compliments!
We will continue to push to lower our emissions in line with the ambitions set, for instance by using biogas and green electricity in our new plant that will go live later this year. Next to the fact that it’s the right thing to do, reducing our emissions gives us more credibility to talk with our customers about their own impact. Positioning us as the leading partner for sustainable farming, helping our customers through current and new innovative products and services to be sustainable successful. I’m really looking forward where this journey will take us next.