Case study: Nutreco's most energy-efficient fish feed plant
Skretting Stokmarknes produces extruded fish feed for salmon and trout and operates the most energy-efficient fish feed plant in Nutreco.
This great performance is the result of years of continuous improvement in processes and operations – taking small steps that added up to major progress over time. The plant's energy- reduction journey started in 2009 (with 2008 as the reference year). Since then, the Stokmarknes team has performed numerous, mainly low-cost, improvements that led to a 19% reduction in energy needed to produce a ton of saleable feed.
In recent years, these efforts have been aligned with Nutreco's overall Operational Excellence program. Considering today's high energy prices, this work has been appreciated more than ever.
The key technical components of Stokmarknes’ success are the plant's high overall efficiency; long production runs; low base load (rate of energy consumption when the factory is not producing); electric boiler, which uses a hybrid heat pump that recovers heat from the dryers’ exhaust air; and many other small in-house solutions for energy recovery. In addition to its state-of-the-art equipment, the expertise of the local team and their passion for continuous improvement has been critical for the plant's overall success.
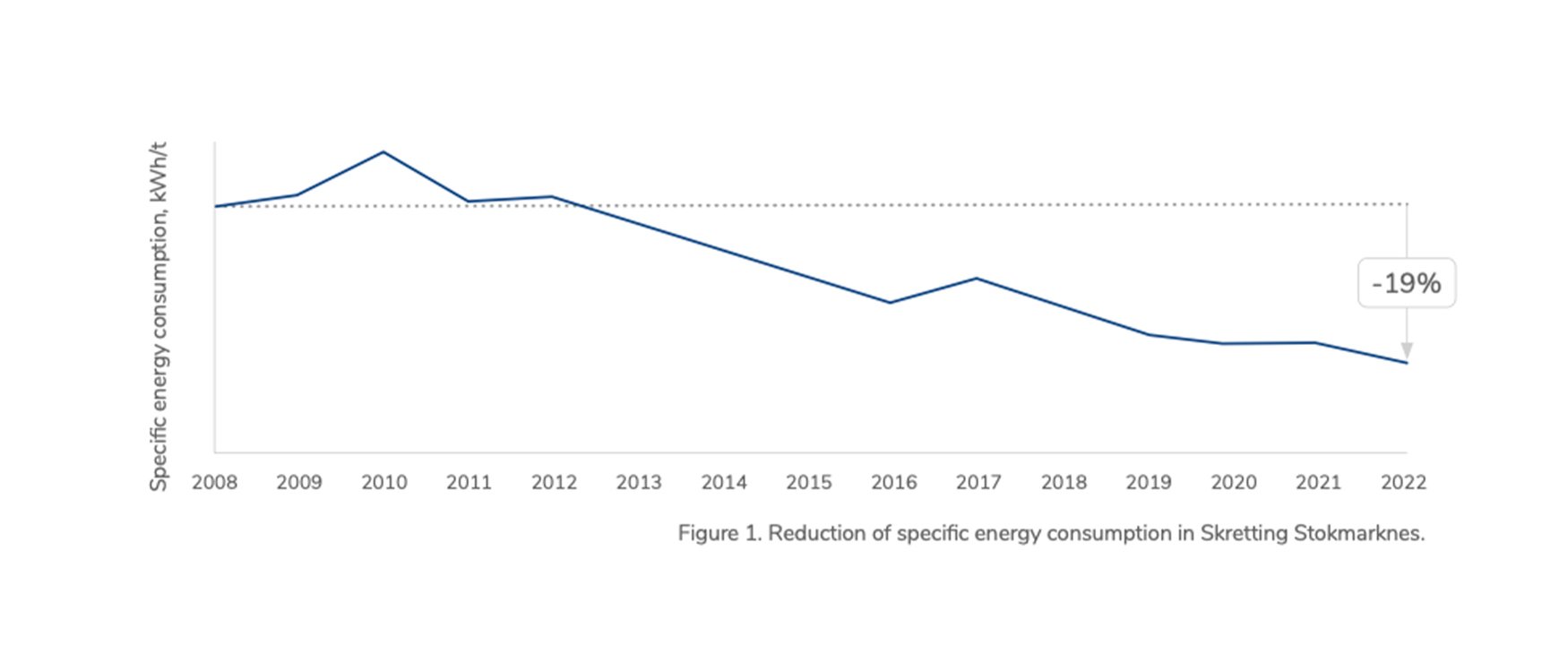
This is partly due to the leadership of Harald Steffensen, who heads up Skretting Norway's energy team, which is challenging the limits on the energy needed to produce fish feed and does not allow any energy-saving opportunity to pass unexplored. Harald Steffensen has worked at Skretting since 1989 and has led the energy team of all three of its factories for the last 14 years.
We asked Harald what was key to Skretting Stokmarknes’ success, and what advice would he have for other plants just starting this journey:
"From 2002 to 2009, Skretting Norway's factories underwent a LEAN improvement process, aimed at reducing waste of resources, time and effort. As technical manager at Stokmarknes, I learned that this helped significantly improve the factory's overall equipment efficiency and made it the most energy efficient in the Norwegian fish feed industry in 2009."
"The Stokmarknes energy team carefully examines every opportunity and idea for energy reduction. We always need to make sure that proposed solutions have good financial and environmental benefits. To perform proper evaluation and identify best practices, it is important to have good data quality."
"That same year, we started intensive energy-reduction work once we had the plant at an overall high level. We established energy teams and monthly reporting, implemented energy management in accordance with ISO 50001, energy meters and monitoring systems. This provided a good foundation for carrying out regular energy surveys and continuous improvement processes."
The first step is to improve overall efficiency, such as yield, availability and throughput, in line with our Nutreco-wide Operational Excellence program. In addition, good data quality is important to help us find further opportunities to improve. So, we need to focus on monthly energy reporting and investing into energy meters and monitoring solutions to measure and compare the equipment efficiency of the most energy- demanding processes. Finally, have a dedicated energy team on site that works systematically according to an agreed level of energy management. And remember to celebrate victories!